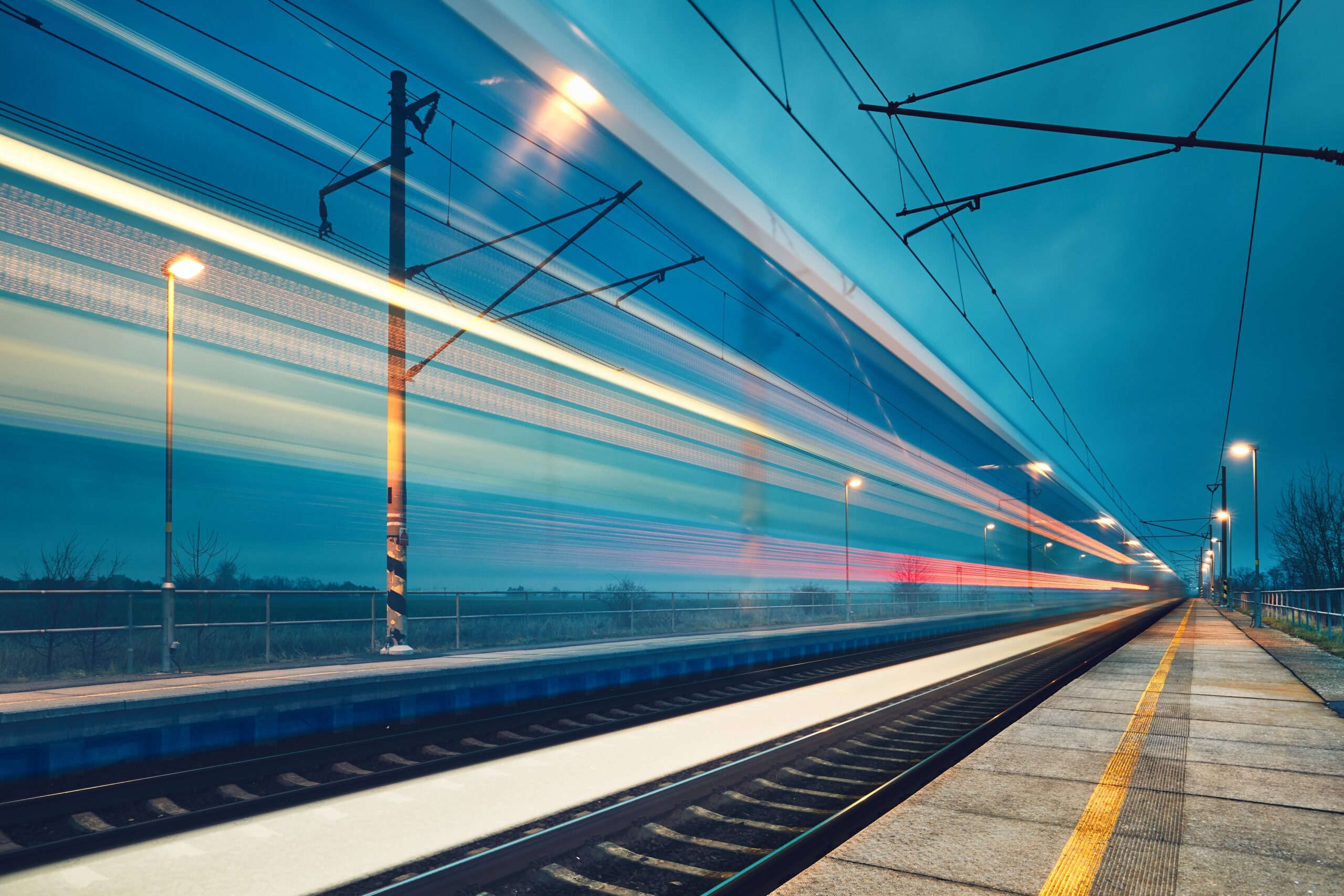
WP 03 – Product Development & Procurement Process
Overall Context
All developed RTR results can be allocated to the Target Process Landscape
With respect to Work Package 03, the initiative aims to shorten the lead time for the rolling stock product development and procurement process.
Main target is to design a process model to which the entire results across all work packages can be allocated to. Main objective of WP03 is to increase efficiency, to enable effective fulfilment of customer needs via proactive product development as well as to reduce the costs related to a tender process and the technical risks and associated costs during the project execution phase.
Within this context, voluntary requirements for mandatory tender documents and potential cooperation formats as well as product dialogues to leverage information exchange between operator and supplier during early stages of the process have been developed, all in compliance with competition law rules.
Being part of the overall RTR Initiative, results from this Work Package have been developed according to the RTR-compliance mechanism (Antitrust Council).
Documents about Product Development & Procurement Process
To download the documents, please log in.
Background
Past tendering processes for railway rolling stock present to be exhaustive, intensive, and inefficient
Today’s process represents a project-oriented approach with major conceptual and development work being started only after awarding of the contract. The total duration from tender initiation to award decision and from award decision to first rolling stock being operated can take six to eight years.
The customer receives customized solutions based on very specific requirements. The frontloading process, namely, to informally exchange information between the operator and the supplier even independently from any tender, is only conducted on ad-hoc basis and not in a structured manner, and in compliance with applicable competition laws. In order to improve the status quo, a set of current challenges has been translated into appropriate requirements to finally derive adequate type of results that support the optimization of the rolling stock product development and procurement process. This will result in greater efficiencies and significant reductions in lead time.
Objectives
Tangible measures with positive effects to reduce lead times and effort
Derived from consolidated issues that RTR members generally observe along product development and procurement processes, several optimization measures were identified. In that context, this work package intended to develop tangible measures with a positive effect on the current process to reduce lead times and effort. Hereby, the focus lies on shifting parts of the conceptual work for both industry sides, manufacturer, and operator, to the early stages of the process as part of a structured but informal (where necessary bilateral between operator and supplier) frontloading process. Furthermore, development work subsequent to awarding shall be significantly reduced to promote a product driven business approach.
Associated measures are clustered along five different categories listed below with a coherent explanation:
- Process
Efficiency and effectiveness improvement of entire process steps in form of reorganizing underlying sequence, associated content and involved parties.
- Standardized description of products/ platforms
Establishment of a product-oriented approach in order to decrease process time and required effort and rework by offering and ordering based on more standardized product descriptions and modules instead of dealing with hundreds of customization requirements.
- Collaboration
Creation of continuous collaboration between operator and supplier starting within an early stage of the process to ensure constant knowledge transfer and reduction of additional coordination and rework effort throughout the entire process.
- Communication
Establishment of continuous industrial dialogues between operator and supplier within early and tender independent stages of the process in order to reduce communication effort and increase transparency about latest technologies and respective needs.
- Documents and Templates
Creation of voluntary requirements sets of reusable tender documents to avoid starting each tender document creation from the scratch and to enable a common and comprehensive understanding of definitions and terms.
Target process framework
Procure less customized but available product variants from the industry.
The process framework (see Figure 1) serves as an overall voluntary guideline, all other deliverables, even from other work packages can be allocated to:
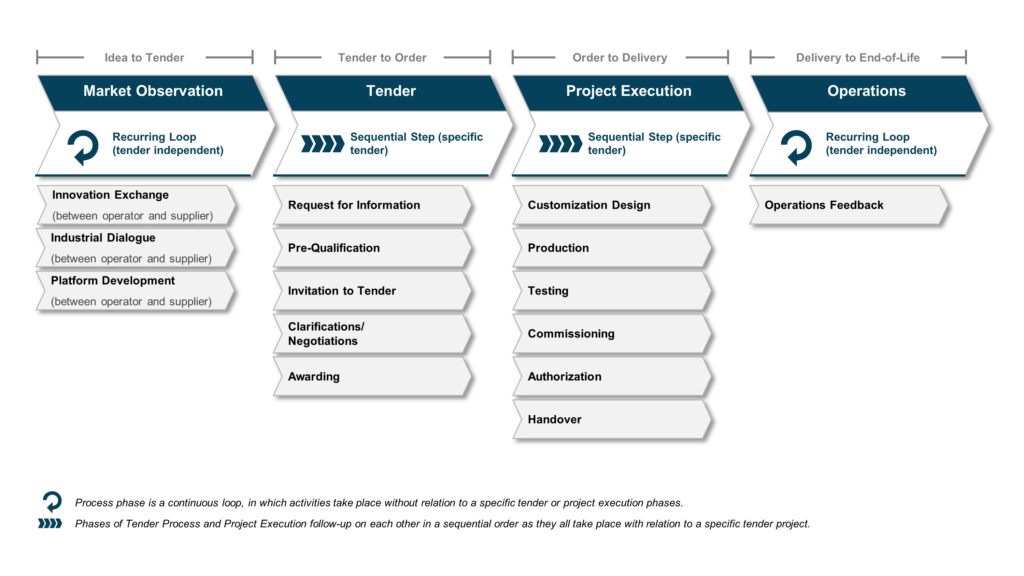
The development of the RTR target process follows the principle to establish a product-oriented market, where operators procure less customized and available product variants from the industry. Therefore, a synchronized nomenclature of the product development and procurement process is defined to guarantee a common understanding about high-level process steps and associated activities.
The RTR target process consists of four different phases starting with the market observation process to informally (and bilaterally) exchange information between operator and supplier, followed by the tender and project execution processes and ending with the operation of the train. In comparison to the processes currently implemented at the member firms, fundamental changes are suggested to take place at the sub-process level.
In particular, development activities within the project execution phase shall already be executed at early stages of the process within the market observation phase. Furthermore, activities that are not time-sensitive such as the (bilateral) discussion on specific requirements between operator and supplier, changes or the clarification about additional pre-defined options can be executed beforehand on a regular basis without extending the time of the actual tender process. Consequently, the entire market observation phase experiences an expansion of its activities regarding the continuous exchange of information, knowledge, and respective requirements between operator and supplier.
This work package does not intend to re-define existing and detailed company internal processes but rather strives to create a unique understanding and to illustrate the most significant changes in comparison to the status quo.
The jointly developed target procurement process creates a harmonized process model to foster innovations and to create a unique understanding about tender, project execution and operations processes, which finally results in numerous benefits:
- Harmonized understanding of all process activities, roles, and responsibilities
- Transparent overview on effort drivers during the tender and project execution processes
- Efficiency and effectiveness as well as improvement
- Continuous collaboration and best practices exchange within early stages of the process between operator and supplier